Game Discription
Two teams of three robots each compete against each other. They go in counterclockwise circles around a center median, while carrying large “Trackballs” over and under overpasses for extra points
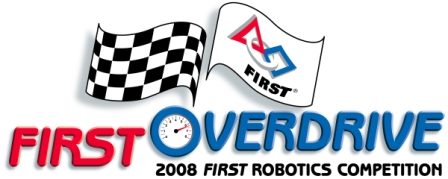
Official Game Rules
FIRST Overdrive is played on a 54′ x 27′ track divided by a fence into a Red side and a Blue side. The fence is crossed by an overpass marking the red and blue finish lines. Two three-team alliances race around the track in a counter clockwise direction manipulating Trackballs. The game is made up of two scoring periods. The first 15 seconds of play is the Hybrid period in which robots are autonomous, and may also respond to digital signals sent by team Robocoaches stationed at the corners of the track. During the Hybrid period, robots traveling in a counter clockwise direction score:
- 8 points for each of their Trackballs knocked off of or passed over the overpass
- 4 points whenever their robot crosses a line on the track
- 2 points whenever their trackball crosses their finish line
The next two minutes of play is the Teleoperated period. At this time, robots are radio controlled by team operators standing at either end of the field. During the Teleoperated period, robots traveling in a counter clockwise direction score:
- 2 points whenever their robot or Trackball crosses their finish line
- 8 points whenever their Trackball passes over their overpass
Alliances score an additional 12 points for each of their Trackballs that are positioned anywhere on the overpass at the end of the match.
Our Robot
Overview
The best feature of our robot is its quick lifting. On our robot, there is also a gripper that is pneumatically driven, and exerts 35 lbs. of force. The drivetrain features are the Omni wheels for turning a tight radius, high traction tires for quick acceleration and improved turning, a 6 wheel suspension system for stability, and 4 powered wheels for increased maneuverability. The software features are a highly tuned drive system, auto height selections for lift, a faster lift speed in hybrid mode, and a hybrid mode. Specialty feature is a telescoping life mechanism for simplicity. Last is the “Safety FIRST,” which means that the forks are blunt, the spring mounted forks move easily, the gripper is flexible to bend when impacted, the gripper’s vertical force will securely hold the ball, and the design is multi- functional for lifting and herding.
Design
The robot design was intentionally kept as simple as possible to allow us to concentrate on perfecting the design. Our conveyor system is a two-staged conveyor system that uses a solid-core round urethane belting. The two stage conveyor system allows us to easily control how many balls we have in our possession and where they are in our system at one time.
Specifications
- Height 59″, Width 33.5″, Length 33.5″, Height mast extended 126″
- Weight 119.0 lbs.
- Speed 12 fps.-Lift trackball in 1.6 seconds!
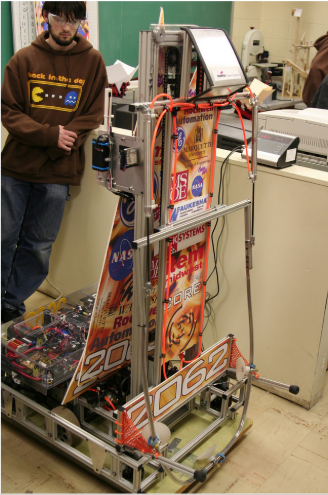
Design
Helios’s design function was to be a multi-purpose robot built to put “Safety First”. The team chose to build in speed, herding ability, a fast lift system, and a simple but highly functional gripper mechanism.
Controls
The controls were also a product designed for “Safety”. Clear visibility, so judges can easily see what is going on in our robot, was an important part of our design. A clear plastic cover ensures visibility of our controls. A hole in the cover lets us access the main circuit breaker to quickly turn our robot off. Swinging covers provide access to critical components to render the robot to a neutral state. The cover also incorporates quick disconnects to easily access the controls for maintenance and repair if needed. The cover can withstand vertical and side impacts to more than 4 times expected forces during the game. A fan provides cooling for all the critical controls components while also providing airflow over the drive motors. The final electrical design allows maximum power to be delivered to all power systems. The components were oversized where practical to allow for this maximum delivery of power! Helios is a fully functioning and completely safe robot.
Programming
The software code is critical to the functionality of Helios. The software allowed for easy operator maneuverability, incorporated critical lifting “Safety” features while maximizing performance on every system. Drivability and maximum controllable lift speed was the key to the overall success of Helios.
Pneumatics
The pneumatic system powers the gripper and allows for ease of use with maximum power delivery through a flexible system. This system compliments the gripper and helps achieve the “Safety First” gripper design
Drive Train
Speed was obtained by using a simple CIM motor, transmission with chain drive system. This drive system was simple to build and maintain. The drive system also achieved high maneuverability with the chain drive, only utilizing the rear 4 wheels. This reduced the turning radius to literally half the length of the robot. Traction wheels were used in the center of the robot and Omni-wheels on the ends. Herding ability was obtained with a simple, flexible lower fork type design. The ball can be easily positioned between the forks as the bend easily to pressures exerted against them but have enough resistance to hold the ball. This allows the ball to slide across the carpeted floor and be herded over the end-line. Dual CIM motors coupled to a standard transmission provide the lifting power for the mast. This design can lift the mast and ball from the floor to a full extension of 10’6” in under 1.6 seconds. At 6.5 ft/sec, this is one of the fastest lifts we have seen. Electrical stops were added for safety at both the upper and lower ends. “Safely” controlling the mass of the lift and ball at both ends makes the game “Safer” for all the robots on the field.
Our Success
2008 St. Louis Regional
Our team started the season at the St. Louis Regional, from February 28th to March 1st. We knew that this was one of the stronger regionals and we wanted to see how we stacked up against some of the best teams in the nation. Our main goal was to get in as much practice time as possible in preparation for the Wisconsin Regional. We were delighted and surprised to do as well as we did amongst the 45 teams attending. We made it to the semi-finals, and we were beaten by the eventual competition winners, an alliance of teams 148, 217 and 830. We would like to thank our alliance partners, teams 525 and 2044. They were great to work with and showed gracious professionalism in the heat of battle. We were extremely proud to bring home three awards from this regional. Our team received the Kleiner Perkins Caufield & Byers Entrepreneurship Award, the Underwriters Laboratory Industrial Safety Award and the Website Award.
2008 Wisconsin Lakes Regional
From March 13th through the 15th, our team attended the Wisconsin Regional. We decided to make a few modifications to the robot after St. Louis. We brainstormed on how to make our adequate robot even better. After our team decided to make a Lexan flipper that enabled us to remove balls faster from the overpass and we ordered different gears that made the robot 50% faster. We knew that changing the gear train would be risky because we had a very limited amount of time to swap out parts in Milwaukee. Luckily, the schedule in Milwaukee worked to our advantage and our great pit crew was able to make all modifications between the preliminary matches. The Wisconsin regional surpassed all of our expectations! We won the regional with alliance partners 171 and 2549. Special thanks go out to team 171 for picking us and assembling a great alliance. Team work was critical, and our alliance performed like they had been working together for a very long time. The memories from Milwaukee will last a lifetime. We were very happy to also win the Underwriters Laboratory Industrial Safety Award for second time. Then, we went off to Atlanta for the FIRST Championship, which was held from April 17th to April 19th.
2008 FIRST Championship
Our team qualified for the 2008 championship by winning the Wisconsin regional with the assistance of teams 171 and 2549. Our entire team was thrilled that our incredible journey would not be ending just yet, but that we were able to continue on to the International Championship in Atlanta, GA. Our team was not chosen for the final matches in our division. We were, however, the winners of the Underwriters Laboratories Industrial Safety Award. Our entire team was thrilled to learn all of our hard work had paid off and that we were the safest team in the world. Our team had an incredible season in 2008 and cannot wait for the 2009 season to begin.
Other Components
- Website team worked on the website, which won an award.
- Safety team made sure the entire robotics team was unharmed. Thanks to their terrific efforts, we won the UL Industrial Safety Award at both regionals and at the Championship.
- Animation team did an amazing job making the safety animation and their annual entry to the Autodesk Visualization Award.
- Awards Won: UL Industrial Safety Award (both regionals and Championship), Kleiner Perkins Caufield & Byers Entrepreneurship Award, and Website Award.